Executive Summary
Levels of phosphorus, a chemical element that promotes organic growth, must be controlled in wastewater coming from beverage, food and dairy processing plants. Failure to control phosphorus accurately has a negative impact on water quality and can lead to large fines. The widespread practice of manually testing effluent only at set time intervals often leads to overdosing or underdosing with chemical control. Overdosing occurs when control continues at the same rate even when phosphorus levels are low. Underdosing happens when phosphorus levels spike in the interval between tests. This sends excess phosphorus into the stream before control measures can be adjusted.
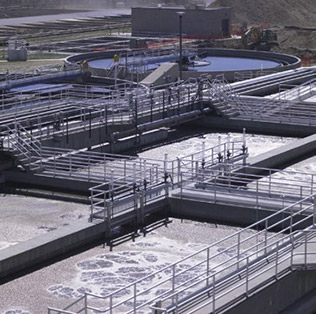
Real-time control offers continuous monitoring to allow accurate dosing, giving plants better control over operations, regulatory compliance and costs. This white paper will describe a system for realtime control and the benefits it offers, specifically for plants that are controlling phosphorus by chemical dosing with ferric chloride (FeCl 3).
The phosphorus problem
The element phosphorus is essential to life and so it is present in plants and animals. The most common food processing sources of phosphorus or phosphates include meat, milk, soy and cleaning agents. Derivatives like phosphoric acid make their way into soft drinks, baking powder, and even toothpaste. Phosphorus promotes growth, which is good for a fertilizer, but bad for wastewater effluent.
When phosphorus is discharged in wastewater from beverage, food and dairy processing plants, usually in the form of PO4, it “fertilizes” algae and aquatic plants so they multiply and deplete the oxygen in streams, rivers and bays, ultimately choking out larger organisms and disrupting the healthy balance of the ecosystem.
Regulations exist to protect water, wildlife and people from uncontrolled amounts of phosphorus in wastewater, and these regulations have an economic impact on beverage, food and dairy processors. There are costs associated with removing phosphorus from wastewater, but there are higher costs associated with failing to remove it adequately or reliably. Most immediate are fines levied by state and EPA regulators. The highest profile are fish kills or algae blooms that impact community water sources. Most lasting are the impacts on the reputation of the beverage or food processor as a neighbor employer and brand.
Clearly, phosphorus must be controlled and discharge limited to safe levels.
Manual monitoring, manual dosing
Wastewater from beverage, food or dairy processing plants usually goes one of two places: directly back into a natural waterway, or to a municipal wastewater treatment plant for further treatment. Permits and regulations vary between the two, and the upper limit for phosphorus depends on location as well.
Traditionally, regulatory agencies test for phosphorus by setting up a water sampler downstream from a processing plant and taking samples at set intervals; for example once per hour. Then this composite sample is tested once a day, and if it exceeds the permitted level of phosphorus, the agency levies a fine. In order to avoid fines, plant operators test their own effluent periodically. The more often they can draw samples, the more accurately they can measure phosphorus over time and dose control agents more precisely. However, the labor cost of manual sampling is multiplied as the number of samples increases, so most sites choose a testing interval and hope that it is frequent enough to detect changes. To compensate, the sites overdose with FeCl 3 to provide a safety margin.
The result of this approach is that sites often use too much or too little chemical and that is when they get fined. If, for example, their allowable limit is 1.0 mg/L, a site may set their dosing levels to achieve 0.8 mg/L based on the average phosphorus content of their effluent, hoping this will be sufficient to control variations. The intent is to reduce risk and uncertainty, but this does not really improve controllability. This strategy uses 20% too much ferric chloride most of time while not controlling sudden phosphorus spikes. Spikes can occur for various reasons. A process changeover or increase in process speed increases water flow, discharging more phosphorus. Cleaning operations might use phosphate-containing detergents and high pressure, high temperature water that can suddenly send higher than average amounts of phosphorus downstream.
In short, plant operators are hit with costs two ways – paying too much for dosing chemicals while still being fined for excess phosphorus.
Real-time Control
Increasing frequency of grab sampling improves the chances of detecting changes in phosphorus levels, but these grab samples only provide a snapshot in time of stream conditions. Dosing rates are based on composites of grab samples over a previous time period, so operators are dosing for past discharges, not the current one.
Fortunately, there is proven technology for automating realtime monitoring and dosing control that can give beverage, food and dairy plant operators the data and control they need to meet regulations without overspending on chemicals. A system of compatible, integrated sample analyzers and dosing controllers all managed from a central control unit takes the guesswork and human error out of phosphorus treatment.
A complete, integrated real-time control system starts with an automatic analyzers. The Phosphax sc Digital Phosphate Analyzer from Hach® can prepare and analyze a sample in under five minutes. Set in a ruggedized weatherproof housing it can be set right at the tank to provide continual, highly precise measurements of phosphorus levels with detection limits as low as 0.05 mg/L. It is designed to use minimal amounts of reagent. Multiple output options are available, making it easily compatible with existing systems.
The analyzer sends
data to a central controller, the Hach SC1000 Multi-Parameter Universal Controller. This solid-state, modular controller can monitor up to eight sensors directly or be networked to monitor 32 sensors, each analyzing different parameters. A large color touchscreen lets operators observe system status quickly. Parameters can be adjusted easily when processes change.
The central controller receives data from the analyzer and sends commands to a Phosphorus Real-Time Controller (RTC-P) that manages the coagulant (typically FeCl 3) dosage in real time. It signals the feed pump to discharge the appropriate amount into the effluent stream.
The Hach RTC-P also includes PROGNOSYS™ software for predictive diagnostics. This subsystem continually monitors the RTC-P system and delivers status alerts so operators can take proactive troubleshooting, maintenance and repair action.
Benefits of real-time control
The main benefit of using real-time control to monitor phosphorus is maintaining compliance with permits thanks to more accurate chemical dosing. Being able to control changing phosphorus levels, even when the concentration fluctuates widely and unexpectedly, reduces risk and variability in effluent discharge.
One dairy plant was able to maintain phosphorus compliance without overdosing ferric chloride. This had the added benefit of reducing dosing by an average of 33%, saving $1863 per month. A soft drinks manufacturer was able to meet their compliance limits. Their phosphate discharge values are now controlled at less than 2 parts per million total phosphorus.
Total suspended solids (TSS) and turbidity readings are also reduced by approximately 10%.
Other savings come from reducing labor costs associated with manual sampling and coagulant pump setting changes. Also, more accurate dosing reduces sludge creation.
Additional benefits come from using a prepackaged, turnkey integrated system composed of proven components. In contrast with house-built solutions that string together various pieces, a turnkey system saves staff resources and time while building on its expertise. It ensures continuity of institutional support rather than relying on one person or a department that will eventually turn over. It also ensures the interoperability and optimization of the components and software. An automated RTC-P system helps plants reduce operational complexity.
In short, automated real-time phosphorus control reduces variability and makes outcomes more predictable and controllable. This is better for both the environment and the bottom line.
How 2 plants stayed compliant and brought chemical costs down
A cheese processing facility with high phosphorus output that varied widely was challenged to stay below the 1.0 mg/L limit required. Peaks as high as more than 4 mg/L were often detected too slowly to manually adjust chemical dosing. Installing real-time control brought stability to the process by dosing the right amount of FeCl 3 at the right time. This kept output under the limit while reducing chemical consumption by 33%. Average savings in chemical costs alone are $1863 per month, not including the savings created by avoiding fines.
A soft drinks manufacturer was able to meet their compliance limits. Their phosphate discharge values are now controlled at less than 2 ppm total phosphorus.
TSS and turbidity readings are also reduced by approximately 10%.
More solutions on improving compliance through real-Time control