Advanced on-line instrumentation provides continuous, real time suspended solids measurement in DAF operations, which automates and optimizes polymer and coagulant feed regardless of wide load variations. The result: potential polymer savings of 20 to 30 percent.
Overview
Many food processors use dissolved air flotation (DAF) to remove fats, oils and grease (FOG) and suspended solids from their wastewater streams. In DAF operations, chemical coagulant and flocculant additions are often required, and dosage rates are typically kept on the high side because of the wide, sudden variations in influent water quality that are characteristic of food processing facilities. Because periodic jar tests can provide a snapshot of loadings current only at the time the sample was pulled, operators typically overfeed coagulant and flocculant to play it safe. This can be an expensive procedure, however.
Advanced on-line instrumentation in DAF operations provides the capability of optimizing system performance while significantly lowering chemical usage. The continuous, real time measurements from these new sensors can provide for automated and optimized chemical feed regardless of wide load variations.
Dissolved Air Flotation (DAF)
In DAF, wastewater first enters a coagulation tube where coagulants and flocculants may be introduced to increase the particle size along with whitewater (a mixture of a portion of the DAF effluent which has been saturated with atmospheric air). The wastewater then enters the vessel across the length of the system, where the water velocity is significantly reduced to maximize separation potential.
The micro-bubbles inside the vessel attach to the particle surface, affecting particle density and causing the suspended solids to fl oat to the surface where they are skimmed off. Heavy particles settle to the bottom and are removed. Clarified liquid is continuously removed from several points in the DAF vessel.
Generally, flotation separation systems such as DAFs can process feed with up to 300 ppm oil content. Without chemical addition, they can remove particles larger than 25 microns. With chemical addition to coagulate oil and solids, particles less than 10 microns can be removed. The effectiveness of the process depends upon a number of factors, including the adherence of the bubbles to the oil, interaction of the oil and gas, the size of the floc and the amount of gas in the floc.
The addition of polymers and coagulants can significantly enhance the performance of DAF units. Commonly used chemicals include trivalent metallic salts of iron, such as FeCI2 or FeSO4 or aluminum, such as AISO4. Organic and inorganic polymers (cationic or anionic) are often used to enhance the DAF process. The polyacrylamides are the inorganic polymers most commonly used. When using ferric compounds, pH should typically be adjusted to between 4.5 and 5.5, or between 5.5 and 6.5 for aluminum compounds using an acid such as H2SO4 or a base, such as NaOH.
Considerable effort has been directed by food processors to optimize the performance of DAFs, and polymer use has received significant attention due to its high cost. Concentrations of chemical flocculants used normally range from 100 to 500 mg/L (1.0 mg/L in one million gallons per day is 8.34 pounds of material). If a processor’s daily flows are 1,000,000 gallons per day (GPD), for example, and chemical feed is 40 ppm, the amount of chemical fed per day is 333 lbs. Based on the cost of the chemical being $ 1.10 per lb., the cost of this treatment is $133,940 per year. A reduction in usage by only a few percentage points can significantly lower costs.
Accurate Chemical Dosage Control Can Be Difficult
Although systems that monitor pH and adjust it by controlling acid or base dosing pumps are commonly used, polymer and coagulant dosage control has typically been a manual operation, based on periodic jar test results and flow pacing. It has been difficult for food processors to find reliable systems for automatically adjusting dosage of coagulants and flocculants for DAF due to influent loadings that can change within minutes.
Because of this, dosage rates are typically set high to ensure high influent loadings are sufficiently treated. When influent water has a low organic load, these chemicals are overfed, often wasting a significant amount of money.
Automatic Dosage Control
Although most DAF operations have long relied on jar testing to obtain suspended solids readings, new online sensors now provide accurate, real-time suspended solids measurements, thereby reducing the reliance on intermittent and time-consuming analysis. The Hach TSS sc probes have a double optical system with two pulsating infrared LEDs and four receivers to monitor the waste stream. As the transmitted light is scattered, the receivers pick up the incident light at 90° and 120° angles, effectively doubling the accuracy of the instrument.
DAF operators can utilize the suspended solids sensor with Hach SC200 Controllers to precisely monitor suspended solids levels in DAF influent and use these ongoing readings to automatically control chemical feed dosage. The signal from the sensor is linked to the plant’s DCS or SCADA system using a full-scale 4-20 mA output from the sensor’s controller. With real-time flow rate, sensor value, and polymer flow and concentration, the DCS/SCADA system calculates and adjusts the polymer or coagulant flow rate to consistently meet the set point of pounds of active polymer to dry ton of mixed sludge.
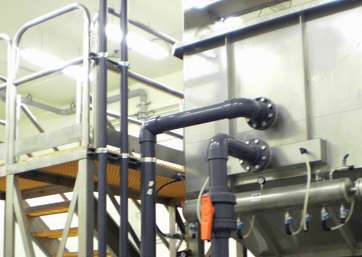
The suspended solids analyzer’s infrared light technique eliminates color interference, minimizes calibration and improves accuracy, and the instrument’s self-cleaning capability prevents erroneous values. Wastewater treatment facilities can use the units to measure suspended solids up to 500 g/L in plant influent, filtrate/ centrate, mixed liquor, final effluent, and primary, digested, and thickened sludge. In addition, the SC200 Controller allows for adjusting the sensor measurement with an operator-entered factor that correlates sensor measurement to traditional gravimetric suspended solids determination. This allows for fine tuning the sensor measurement. Operators can revise this factor at any time as required due to changes in overall water quality conditions.
The Goal: Reduced Chemical Consumption
Although systems that monitor pH and adjust it by controlling acid or base dosing pumps are commonly used, polymer and coagulant dosage control has typically been a manual operation, based on periodic jar test results and flow pacing. It has been difficult for food processors to find reliable systems for automatically adjusting dosage of coagulants and flocculants for DAF due to influent loadings that can change within minutes.
Because of this, dosage rates are typically set high to ensure high influent loadings are sufficiently treated. When influent water has a low organic load, these chemicals are overfed, often wasting a significant amount of money.
FOR TECHNICAL ASSISTANCE, PRICE INFORMATION AND ORDERING:
Tel: 800-227-4224 | E-Mail: techhelp@hach.com
To locate the HACH office or distributor serving you, visit: hach.com
Are you interested in more information about our solutions for food? Click here.